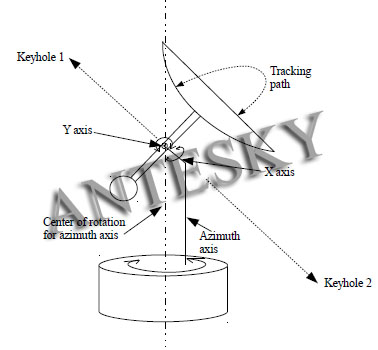
Copyright © www.antesky.com3-axis X-Y Pedestal for LEO/MEO Tracking Ka-band Antenna : A very unique and efficient pedestal design, that has been optimized for tracking LEO satellite on ka-band frequency. It has a novel three axis geometry that not only provides for full hemispherical coverage but also assures that during tracking. The system never comes closer than 45 degrees to a keyhole. This leads to the lowest possible axis speeds and accelerations while enabling the system to accurately track the satellite. With the development of the space industry towards big constellations of LEO satellites that produce huge amounts of data. Ka-band is gaining momentum. We need significant contact time which translate into a large network of antennas distributed globally for serving large constellations of satellites . The low power capabilities of small satellite and we end up with the demand for large dish diameter to provide an adequate link budget. With traditional pedestal geometries, the cost of system to meet the demands for LEO Ka-band tracking with large dish diameters become expensive. While designing the antenna system around our novel pedestal, one of the main goals was a minimum lifecycle cost.
Many companies built satellite tracking antennas for LEO satellites in the late 1950s, with little change except for the use of modern electronic devices. However, with the recent changes in the small satellite industry and rapid economic growth, the demand for the ground component is also changing. As satellite constellations tend to produce large amounts of data at a large and low cost-effective scale, the ground component must follow a cost-effective network. High availability, the ground station will be able to provide sufficient contact time to download all data. Given the low power budget of small satellites and the need to use higher frequency bands, the requirements of the ground station will include large apertures, high-precision tracking and the ability to operate in the Ka/Ku band. To provide a larger aperture size for these frequencies, the following issues need to be addressed:
Various ground stations will require interpret ability and central control
Faster relative angular velocities are needed to track lower and decaying orbits and present a unique challenge, near keyholes where axis velocities increase exponentially.
Reduced beams widths of higher frequencies coupled with larger apertures require higher pointing accuracy.
Smaller wavelengths require tighter requirement on reflector geometry and on deformation of the reflector caused by weight, wind loading and uneven thermal gradiants;
Smaller wavelengths have an increased sensitivity to moisture and require much greater margins to compensate for its effects.
Specialized custom components result in higher cost. longer MTTR and frequently. lower reliability:
Complex multi-motor drive system to control backlash result in higher complexity and cost while reducing reliability.
Antenna location require protection of the antenna system from extreme environments.
The high volume of small satellites and the corresponding demand for additional ground stations require that both initial cost and day-to- day operating costs be driven down.
To address these issues, the ground station needs to support the most advanced technologies and protocols as much as possible. In addition, the pedestal environment control is required. By controlling the internal pedestal environment, you can ensure uniform and predictable movements while increasing the life expectancy of components.
A new pedestal geometry which allows use of a single mode of operation while never approaching a keyhole to within 45 degrees, minimizing requirements for axis velocities and accelerations:
A single motor zero-backlash gear reduction system which allows a single motor per axis to control each axis.
Forit’s lean design it has to be protected by a radome. A special very low loss radome construction was developed.
Ultra-high integration.
Advanced
In addition to these innovations, we also considered how to improve other major ground station components. That is, the servo drive. Parabolic reflectors, feed and control software. The result is a new and innovative ground station that can handle current and future requirements in virtually any weather condition with the highest possible life cycle cost.
THE POSITIONER
The tracking antennas, relied on Az-El geometry, has a keyhole in the zenith, which presented a problem for tracking a high fixation passes. For overcoming this, new geometries were introduced. X-Y geometry moved the keyholes to the horizon and thus often had problems tracking at low. elevations.X-Y over Azimuth is a geometry that acts as X-Y or Az-El depending on a pass geometry but adds a lot of complexity and cost to the system. Other geometries such as Az-El- crosslevel which enables the Az-El type of positioner to avoid the zenith keyhole. but only by a few degrees which is far from optimal and again adds a lot of complexity and cost to the system.
Our new antenna positioner geometry works like a two axis X/Y antenna with a Z axis for pro grammatically optimizing the X/Y geometry. The significant difference is that the X axis is tilted at a 45 degree angle from the horizontal. Thus the Y axis angle operates in a range between -45 to 45 degrees perpendicularly to die X axis. This results in the elevation angle transitioning from 90 degrees (die zenith) down to zero(the horizon) when the X axis angle is zero (see Fig. 1). This i$ not nearly as straight forward when the X angle deviates from zero and makes for some interesting math in resolving pointing angles. The result is that the X-axis keyholes are 45 degrees below the horizon and 45 degrees past the zenith. This means that when tracking a satellite. The positioner never gets within 45 degrees of a keyhole.
Since the velocities increase exponentially as a keyhole is approached, this results in significantly lower axial maximum velocities.
For normal polar or weather satellite, this translates to a typical maximum axis velocity of under 0.7 degrees per second. For a CubeSat about 10 re-enter the atmosphere it can be as high as 1.2 degrees/ second. In another way, in the worst case situation while tracking a typical LEO satellite, the X-axis will accelerate from 0 to 0.7 degrees per second and back again over a period of more than 10 minutes. These very low velocities and associated accelerations virtually eliminate the need to consider dynamic effects, allowing the servo loops to be finely tuned for very high accuracy and precision. With velocities are reduced, even time precision becomes slightly less important. This results make a big advantage if TLE’sever become stale, as time is normally the parameter that drifts the most as TLE data becomes old. As an added advantage, the new geometry is structurally very stiff. It has very little counter levered mass resulting in a stiffness approaching that of a classical AZ/EL design. Increased high use of carbon fiber, which is twice as hard as aluminum, resulting in a very hard design. The third major advantage of this design is the use of the Z-axis. It keeps the Y displacement at a minimum angle, i.e. orthogonal as possible, which minimizes axis speed and maximizes the effectiveness of automatic tracking. In our system, those auto-track vectors apply only to X and Y axes. The azimuth is always procedurally controlled based on the satellite orbit in order to minimize the Y angle. In addition, the design’s pointing is so precise that error data collected during automatic tracking can be used to propagate TLE at a time when the update is unavailable. New pedestal shown in both keyholes as below.