High-precision antennas are the key equipment of the satellite communication system, especially for high-frequency antennas such as Ka band antenna.
The main reflector surface of large and medium-sized antennas is composed of dozens or even hundreds of single panels. The accuracy of a single panel is the basis of the accuracy of the antenna’s main reflector surface. Generally, the accuracy of the main surface of C, Ku band antenna and other band antennas is required to be 0.6~0.7mm (r.m.s). The single panel is stretched on a stretched film, and then riveted on the envelope riveted tire. The accuracy of the panel can reach 0.2~0.3mm (r.m.s). The ka-band antenna surface accuracy requirement is 0.2~0.3mm (r.m.s), and the accuracy requirement of a single panel is 0.11mm (r.m.s). For such a high surface accuracy, the traditional molding technology obviously cannot meet the requirements. On the basis of traditional technology, we have developed a new high-precision panel forming technology, that is negative pressure forming technology.
1.Introduction of negative pressure forming technology
The main reflector panel of the large and medium-sized antenna is riveted or glued by the skin and ribs, and the material is generally duralumin.
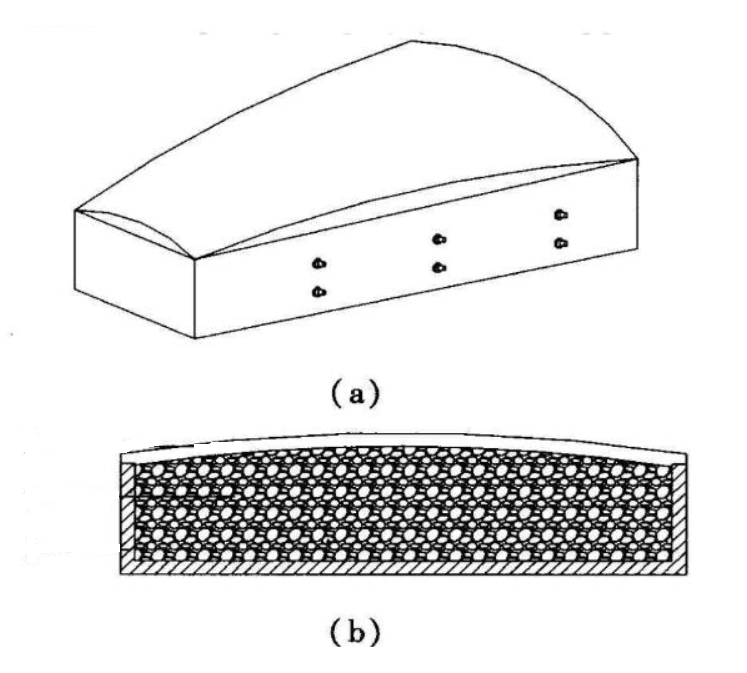
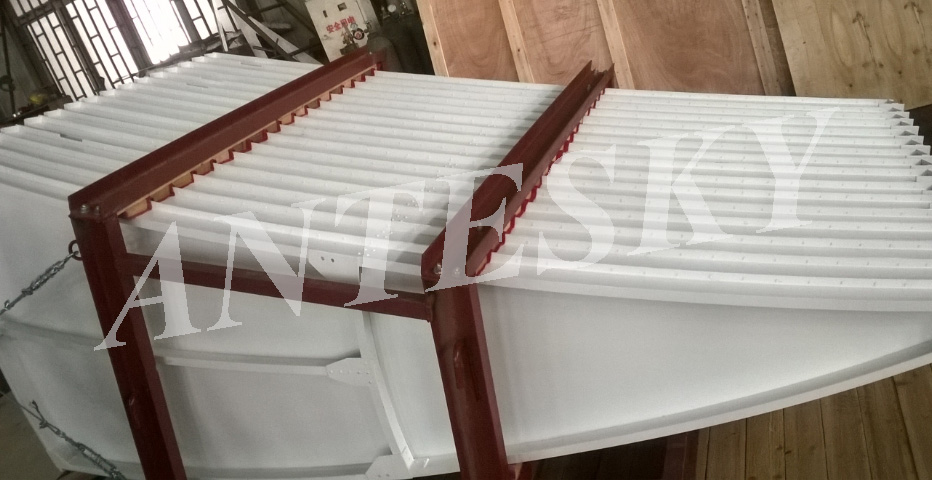
Copyright ©
www.antesky.comThe skin of the panel is stretched and formed on the skin stretching template. After trimming and shaping, the skin is vacuum-adsorbed on the high-precision negative pressure forming template, and the stretched high-precision ribs are combined with the high-precision negative pressure molding with room temperature curing glue. After the skins are glued together and cured at room temperature, 3 to 4 rivets are removed from the mold and riveted on each rib to form a high-precision panel, as shown in Figure 1.
2.Production process of negative pressure forming
2.1 Manufacturing of high-precision vacuum suction mold tires
Adsorption mold tire is the basic mold for panel molding, used for skin stretching and panel negative pressure molding. Therefore, the mold must have sufficient rigidity and precision, and the temperature deformation coefficient of the material must be as small as possible.
Design of vacuum adsorption mold tire
The vacuum suction mold tire adopts a box-type cast steel structure. In order to increase the rigidity of the mold, how to add “#”-type reinforcing ribs in the box structure, and 120mmX120mm of <3mm adsorption holes are evenly distributed on the mold surface to ensure the adsorption accuracy of the skin and mold tires.
Manufacturing of vacuum suction mold tire
The surface accuracy of the vacuum suction mold tire is required to be 0.3mm (r.m.s), and the accuracy is high. In order to ensure the accuracy of the mold tire, the following manufacturing process is determined;
Casting Blank—Annealing—Assembly Welding Blank—Annealing (Artificial Effect)—Natural Aging—Rough Machining—Annealing—Finishing— Measuring Machine Inspection — Fitter Polishing — Retest
When casting the blank, the wooden mold casting and the process plan of correcting the thermal deformation are used, which finally ensures the uniform machining allowance of the castings. The process that combines artificial aging and natural aging not only ensures the stability of the mold tire, but also ensures the processing cycle of the mold. In the mold processing, the rough and fine processing is selected separately, especially in the finishing stage, the precision CNC milling machine is used for processing, and the process plan of the fitter to polish the high points according to the test data, and finally ensure the accuracy of the vacuum adsorption mold tire. The accuracy reaches 0.024mm (r.m.s), which meets the requirements.
2.2 Manufacturing of rib stretching and pressing tooling
Rib stretching mould
The panel ribs are formed by stretching ribs on the rib stretching mould. In order to reduce the influence of the environmental temperature difference on the rib sticking mold, the rib drawing mold is made of carbon steel, just like the vacuum adsorption mold. The manufacturing error requirement of the rib drawing mould is 0.03mm (r.m.s), the ring rib mould is processed by vertical lathe, and the longitudinal rib mould is processed by CNC milling, and all meet the requirements after testing.
Compact tooling manufacturing
C and Ku band antenna panel compression tooling generally use rigid compression. high-precision panel requires high precision, rigid compression and will cause uneven compression force local deformation of the skin or ribs. So the special elastic compression tooling is equipped with a adjustable spring at each compression head position. The compression force can be adjusted to achieve a good performance by adjusting the length of the spring.
2.3 Selection of Structural Adhesive
Structural adhesive directly affects the rigidity, service life and stability of the panel. In order to improve the reliability of antenna panel, the adhesive with high bonding strength, strong resistance to atmospheric aging and good water resistance should be used when selecting. In order to facilitate the operation when bonding the antenna panel and be suitable for the production of large workpieces, room temperature curing glue should be used, and the curing time should be relatively short, and the glue with a certain operating time.
2.4 Ka band Antenna Panel production process
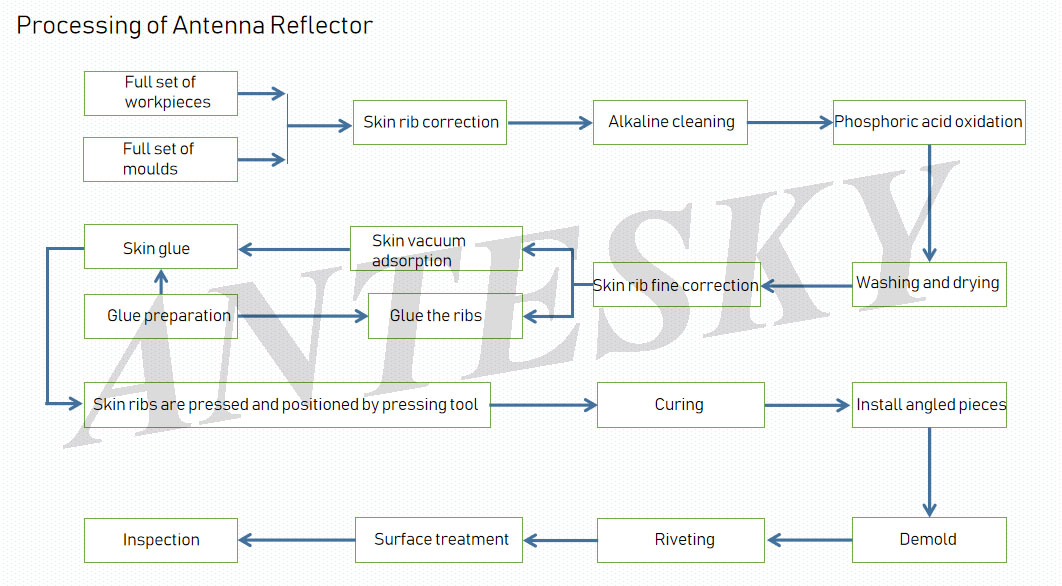
Copyright ©
www.antesky.comDiagram of panel production process for Ka band antenna
The panel manufacturing process is the basis to ensure the accuracy and service life of the panel. The vacuum adsorption panel forming process is a brand new process. We have developed the process shown in Figure 2 for reference.
Skin stretch forming and rib correction
The accuracy of skin and rib will affect panel accuracy to some extent. Before the panel is formed, the skin needs to be calibrated on the vacuum suction mold, and the ribs need to be calibrated on the rib drawing mold.
Skin vacuum adsorption
The skin is aligned on the vacuum forming mold, and vacuum is pumped with a vacuum pump. The maximum non-mold gap between the skin and the mold tire is less than 0.5mm.
Rib gluing and fixed
The surface of the ribs must be coated evenly, and the gluing must be completed in a short time. The rubber strips are fixed on the vacuum forming mold with elastic rigorous tooling, and the length of the elastic compression tool spring is adjusted to make the compression force suitable.
Curing
The curing temperature should be consistent with the temperature of processing and testing the vacuum adsorption mold, and the temperature difference should not exceed 5°C. In the state of vacuum adsorption, keep for a period of time until the glue is basically solidified before other processes can be carried out.
Riveting panel
The number of rivets will directly affect the accuracy of the panel. When riveting, the position and number of rivets on the panel must be determined reasonably, that is, one rivet is riveted at each end of the rib for short ribs, and one rivet is riveted at both ends of the ribs and the middle of the ribs for long ribs.
Surface treatment
When applying glue, sufficient glue should be applied to ensure that the glue fills the joint surface. The excess glue squeezed out during assembly needs to be scraped off or scraped into an uniform shape, which is tightly attached to the glue seam. This work should be carried out before the glue is not cured.
2.5 Inspection of panel accuracy
The accuracy of the single panel of the Ka-band antenna requires about 0.1mm (r.m.s). The traditional measuring method of level and height ruler